Hướng dẫn toàn diện về cách thiết lập dụng cụ cắt tiện
Thiết lập một công cụ cắt máy tiện là một kỹ năng cơ bản đối với bất kỳ thợ máy nào, đặc biệt là khi làm việc với các máy tiện Điều khiển số máy tính (CNC). Cài đặt công cụ thích hợp là rất quan trọng để đạt được kết quả gia công chính xác và chính xác. Trong hướng dẫn toàn diện này, chúng tôi sẽ đi sâu vào các chi tiết phức tạp về cách thiết lập công cụ cắt máy tiện để tiện CNC. Từ những kiến thức cơ bản về các bộ phận của dụng cụ tiện đến các kỹ thuật nâng cao để tối ưu hóa hiệu suất cắt, bài viết này nhằm mục đích cung cấp sự hiểu biết toàn diện về quy trình. Khi kết thúc hướng dẫn này, bạn sẽ có kiến thức và kỹ năng cần thiết để thiết lập một công cụ cắt máy tiện một cách tự tin và chính xác, đảm bảo kết quả tối ưu trong nguyên công tiện CNC của bạn.
Tìm hiểu về dụng cụ cắt tiện
Trong thế giới gia công, dụng cụ cắt tiện là thành phần không thể thiếu để định hình và biến đổi nguyên liệu thô thành các bộ phận được gia công chính xác. Cho dù bạn đang làm việc với máy tiện thủ công truyền thống hay máy tiện CNC tiên tiến, việc hiểu biết thấu đáo về các công cụ cắt máy tiện là điều cần thiết. Trong phần này chúng ta sẽ đi sâu hơn vào đặc điểm, chức năng và các loại dụng cụ cắt tiện.
Đặc điểm của dụng cụ cắt tiện
Dụng cụ cắt tiện được thiết kế để thực hiện nhiều nguyên công gia công khác nhau, chẳng hạn như tiện, tiện mặt, tạo rãnh, tiện ren, v.v. Những công cụ này có chung một số đặc điểm sau:
- Độ cứng: Dụng cụ cắt tiện thường được làm bằng thép tốc độ cao (HSS), cacbua hoặc các vật liệu dụng cụ chuyên dụng khác. Những vật liệu này được chọn vì độ cứng của chúng, cho phép dụng cụ chịu được nhiệt độ và áp suất cao tạo ra trong quá trình cắt.
- Cắt cạnh: Lưỡi cắt của dụng cụ tiện là phần thực sự loại bỏ vật liệu khỏi phôi. Nó được thiết kế sắc nét và chính xác, đồng thời hình dạng của lưỡi cắt có thể khác nhau tùy thuộc vào nhiệm vụ cụ thể mà công cụ này hướng tới.
- Chân: Cán của dụng cụ tiện là bộ phận được kẹp vào giá đỡ dụng cụ. Nó cung cấp sự ổn định và độ cứng cho công cụ trong quá trình quá trình chạy máy. Thiết kế cán có thể khác nhau tùy theo loại dụng cụ và thông số kỹ thuật của nhà sản xuất.
- Giá đỡ dụng cụ: Giá đỡ dụng cụ là một bộ phận quan trọng, đặc biệt là trong tiện CNC, vì nó giữ dụng cụ tiện tại chỗ một cách an toàn. Nó phải cung cấp sự ổn định, độ chính xác và dễ điều chỉnh để đảm bảo hiệu suất công cụ tối ưu.
- Hình học: Hình dạng của dụng cụ cắt, bao gồm góc trước, góc hở và bộ phận ngắt phoi, đóng một vai trò quan trọng trong việc xác định hiệu suất của dụng cụ. Hình học phù hợp là điều cần thiết để đạt được hiệu quả loại bỏ vật liệu và thoát phoi.
- Lớp áo: Nhiều dụng cụ cắt tiện có lớp phủ chuyên dụng, chẳng hạn như TiN (Titanium Nitride) hoặc TiAlN (Titanium Aluminium Nitride), để nâng cao tuổi thọ dụng cụ, giảm ma sát và cải thiện hiệu suất.
Chức năng của dụng cụ cắt tiện
Dụng cụ cắt tiện thực hiện một số chức năng cơ bản trong quá trình gia công:
- Loại bỏ vật liệu: Chức năng chính của dụng cụ cắt tiện là loại bỏ vật liệu khỏi phôi. Việc loại bỏ này có thể xảy ra thông qua việc tiện (xoay phôi trong khi cắt), mài mặt (tạo bề mặt phẳng) hoặc các thao tác khác.
- Kiểm soát kích thước: Dụng cụ cắt có trách nhiệm đảm bảo rằng kích thước của bộ phận gia công phù hợp với các thông số kỹ thuật mong muốn. Kiểm soát chính xác là điều cần thiết để đạt được kết quả chính xác và nhất quán.
- Surface Kết thúc: Chất lượng hoàn thiện bề mặt được xác định bởi độ sắc nét, hình học của dụng cụ cắt và các thông số cắt được sử dụng. Một công cụ cắt được bảo trì tốt và thiết lập đúng cách sẽ góp phần mang lại bề mặt mịn và mịn.
- Kiểm soát chip: Kiểm soát chip hiệu quả là điều cần thiết để ngăn ngừa sự tích tụ chip và duy trì môi trường làm việc sạch sẽ và an toàn. Bộ ngắt phoi trên một số dụng cụ giúp loại bỏ phoi dễ dàng hơn.
- Hiệu suất: Dụng cụ cắt tiện được thiết kế để làm cho quá trình gia công hiệu quả và tiết kiệm chi phí. Chúng giúp giảm thiểu lãng phí vật liệu và tối ưu hóa tuổi thọ của dụng cụ, giảm chi phí sản xuất.
Các loại dụng cụ cắt tiện
Dụng cụ cắt tiện có sẵn nhiều loại, mỗi loại được thiết kế riêng cho các nhiệm vụ gia công cụ thể. Dưới đây là một số loại phổ biến:
- Dụng cụ tiện: Những công cụ này rất linh hoạt và được sử dụng cho các nguyên công tiện hình trụ. Chúng có thể định hình bề mặt bên ngoài và bên trong của phôi.
- Công cụ nhàm chán: Các công cụ khoan được sử dụng để phóng to hoặc hoàn thiện các lỗ hiện có. Chúng được thiết kế để mang lại độ chính xác và chính xác trong gia công lỗ.
- Công cụ chia tay: Dụng cụ chia tay được sử dụng để tách phôi ra khỏi phôi lớn hơn. Họ tạo ra các đường phân khuôn xác định với mức lãng phí tối thiểu.
- Công cụ tạo luồng: Dụng cụ tạo ren được sử dụng để cắt ren trên phôi. Chúng có nhiều hình dạng và kích cỡ khác nhau cho các yêu cầu luồng khác nhau.
- Công cụ tạo rãnh: Dụng cụ tạo rãnh tạo ra các rãnh hoặc rãnh trên phôi, thường để chứa các vòng chữ O, vòng giữ hoặc các tính năng khác.
- Công cụ đối mặt: Dụng cụ đối mặt được thiết kế để tạo ra các bề mặt phẳng ở phần cuối của phôi. Chúng thường được sử dụng để đạt được các bề mặt vuông góc hoặc loại bỏ vật liệu khỏi đầu phôi.
Hiểu các đặc điểm và chức năng của dụng cụ cắt máy tiện là điều cần thiết để chọn đúng công cụ cho một nhiệm vụ gia công cụ thể. Việc lựa chọn dụng cụ cắt có thể tác động đáng kể đến chất lượng và hiệu quả của quá trình gia công, khiến nó trở thành một quyết định quan trọng trong bất kỳ hoạt động máy tiện nào. Ngoài ra, việc bảo trì và thiết lập công cụ thích hợp là rất quan trọng để đảm bảo kết quả nhất quán và chính xác, điều này sẽ được thảo luận chi tiết hơn sau trong hướng dẫn này.
Các loại dụng cụ cắt tiện
Dụng cụ cắt tiện có nhiều loại khác nhau, mỗi loại được thiết kế đặc biệt cho một nhiệm vụ gia công cụ thể. Hiểu các loại công cụ cắt khác nhau này và ứng dụng của chúng là điều cần thiết để chọn công cụ phù hợp cho một công việc nhất định. Dưới đây là một số loại dụng cụ cắt máy tiện phổ biến:
Dụng cụ tiện:
- Công cụ mũi tròn: Được sử dụng cho các hoạt động tiện đa năng. Nó có lưỡi cắt tròn và phù hợp cho cả cắt thô và cắt tinh.
- Công cụ kim cương: Được đặt tên theo lưỡi cắt hình kim cương, nó lý tưởng để gia công chính xác trên nhiều vật liệu khác nhau, bao gồm cả kim loại và nhựa.
- Công cụ mũi vuông: Có lưỡi cắt vuông và thường được sử dụng cho các nguyên công quay mặt và xoay vai.
Công cụ nhàm chán:Thanh nhàm chán bên trong: Được sử dụng để phóng to và hoàn thiện các lỗ hiện có trên phôi. Nó được thiết kế cho độ chính xác và có thể tạo ra kích thước bên trong chính xác.
Công cụ chia tay:Lưỡi chia tay: Những công cụ này được sử dụng để cắt phôi từ phôi lớn hơn. Họ tạo ra một đường chia tay xác định với mức lãng phí tối thiểu.
Công cụ tạo luồng:
- Dụng cụ cắt ren: Được thiết kế để tạo ren ngoài trên phôi. Chúng có nhiều hình dạng và kích cỡ khác nhau cho các yêu cầu luồng khác nhau.
- Công cụ theo dõi chủ đề: Được sử dụng để theo đuổi hoặc khôi phục các chủ đề hiện có. Những công cụ này thường được sử dụng để sửa chữa ren.
Công cụ tạo rãnh:Công cụ tạo rãnh: Những công cụ này tạo ra các rãnh hoặc hốc trên phôi, thường để chứa các vòng chữ O, vòng giữ hoặc các bộ phận khác.
Công cụ đối mặt:Công cụ đối mặt: Được sử dụng để tạo các bề mặt phẳng ở đầu phôi. Nó thường được sử dụng để đạt được các bề mặt vuông góc hoặc loại bỏ vật liệu khỏi đầu phôi.
Công cụ chia tay và tạo rãnh:Công cụ kết hợp: Những công cụ đa năng này được thiết kế cho cả nguyên công chia cắt và xẻ rãnh, tiết kiệm thời gian và thay đổi công cụ.
Công cụ tạo ren và tạo rãnh:Công cụ tạo ren và tạo rãnh kết hợp: Lý tưởng cho các công việc yêu cầu cả nguyên công cắt ren và tạo rãnh trên cùng một phôi.
Công cụ vát cạnh:Công cụ vát mép: Được sử dụng để tạo các vát hoặc các cạnh vát trên phôi. Vát thường được áp dụng để cải thiện hình thức bên ngoài và dễ dàng lắp ráp các bộ phận gia công.
Công cụ khía:Công cụ khía: Knurling là một quá trình tạo ra một mẫu kết cấu trên phôi, thường để cải thiện độ bám hoặc tính thẩm mỹ. Công cụ khía có nhiều kiểu dáng và kiểu dáng khác nhau.
Công cụ tạo hình:Công cụ biểu mẫu: Những công cụ này được thiết kế tùy chỉnh cho các hình dạng bộ phận cụ thể, thường được sử dụng để tạo ra các hình dạng phức tạp và không chuẩn.
Công cụ chuyên khoa:Công cụ hồ sơ: Được sử dụng để tạo các biên dạng phức tạp trên phôi.
Dụng cụ tiện và tiện: Chúng được thiết kế cho cả hoạt động quay mặt và quay.
Công cụ cắt: Được thiết kế để cắt xuyên qua phôi nhằm tạo ra các bộ phận riêng biệt hoặc loại bỏ vật liệu dư thừa.
Việc lựa chọn dụng cụ cắt phù hợp phụ thuộc vào các yếu tố như vật liệu được gia công, độ hoàn thiện mong muốn, kích thước yêu cầu và thao tác cụ thể đang được thực hiện. Điều cần thiết là chọn công cụ thích hợp và bảo trì nó đúng cách để đảm bảo gia công hiệu quả và chính xác. Lựa chọn công cụ phù hợp, cùng với việc thiết lập và điều chỉnh chính xác, là rất quan trọng để đạt được kết quả chất lượng cao trong vận hành máy tiện.
Các thành phần của dụng cụ cắt tiện
Dụng cụ cắt tiện là một dụng cụ chính xác được thiết kế để tạo hình, cắt và loại bỏ vật liệu khỏi phôi. Để hiểu cách thức hoạt động và cách thiết lập nó đúng cách, điều quan trọng là phải làm quen với các thành phần khác nhau của nó. Dưới đây là các thành phần chính của một công cụ cắt máy tiện:
- Giá đỡ dụng cụ:Giá đỡ dụng cụ là bộ phận giữ chặt dụng cụ cắt tại chỗ. Nó gắn vào trụ công cụ của máy tiện và cung cấp độ cứng và độ ổn định cần thiết cho các hoạt động gia công. Giá đỡ dụng cụ có nhiều kiểu dáng khác nhau để phù hợp với các loại dụng cụ cắt khác nhau.
- Chân:Cán là một bộ phận của dụng cụ cắt lắp vào bộ phận giữ dụng cụ. Nó thường có dạng hình trụ và được kẹp chắc chắn bên trong giá đỡ. Kích thước và hình dạng của cán có thể thay đổi tùy theo loại và thiết kế dụng cụ.
- Cắt cạnh:Lưỡi cắt là phần sắc của dụng cụ tiếp xúc và loại bỏ vật liệu khỏi phôi. Chất lượng của lưỡi cắt và hình dạng của nó ảnh hưởng đáng kể đến hiệu suất cắt và độ bóng bề mặt. Điều cần thiết là duy trì độ sắc nét và độ chính xác của lưỡi cắt.
- Chèn:Nhiều dụng cụ cắt hiện đại sử dụng hạt dao có thể thay thế được, thường được làm bằng vật liệu cứng như cacbua hoặc gốm. Những hạt dao này có hình dạng cắt và được cố định trong một túi trên dụng cụ cắt. Chúng có thể được xoay hoặc thay thế khi bị mòn hoặc hư hỏng, giúp kéo dài tuổi thọ của dụng cụ.
- Mũi công cụ:Mũi dụng cụ chính là đầu của dụng cụ cắt, nơi lưỡi cắt và hạt dao (nếu được sử dụng) gặp nhau. Mũi dao phải được định vị và căn chỉnh chính xác để gia công chính xác. Một số dụng cụ cắt máy tiện có bán kính mũi dao có thể điều chỉnh để kiểm soát tốt hơn hiệu suất của dụng cụ.
- Sườn công cụ:Sườn dụng cụ là bề mặt bên của dụng cụ cắt không phải là một phần của lưỡi cắt. Các góc hở thích hợp trên sườn dụng cụ đảm bảo thoát phoi và giảm ma sát giữa dụng cụ và phôi.
- Mặt cào công cụ:Mặt cào là bề mặt của dụng cụ cắt đối diện với phôi. Góc và tình trạng của mặt trước ảnh hưởng đến sự hình thành phoi và hiệu quả của quá trình cắt. Góc trước là một khía cạnh quan trọng về hình dạng của dụng cụ.
- Góc cứu trợ công cụ:Góc sau là góc giữa sườn dụng cụ và trục của dụng cụ. Nó đảm bảo rằng lưỡi cắt không cọ xát vào phôi, giảm ma sát và sinh nhiệt.
- Góc giải phóng mặt bằng công cụ:Góc hở là góc giữa mặt trước và bề mặt phôi. Nó cho phép phoi di chuyển trơn tru và ngăn chặn sự can thiệp giữa dụng cụ và phôi.
- Máy cắt chip (nếu có):Một số dụng cụ cắt, đặc biệt là những dụng cụ được sử dụng cho nguyên công gia công thô, có bộ phận ngắt phoi, rãnh hoặc khía trên mặt cào. Bộ ngắt phoi giúp kiểm soát sự hình thành phoi và cải thiện việc thoát phoi.
Việc lắp ráp, căn chỉnh và bảo trì đúng cách các bộ phận này là điều cần thiết để đạt được độ chính xác và hiệu quả gia công. Việc lựa chọn dụng cụ cắt và thiết lập nó phải được điều chỉnh phù hợp với hoạt động gia công cụ thể và vật liệu đang được gia công. Việc kiểm tra và bảo trì thường xuyên các bộ phận của dụng cụ cắt cũng cần thiết để đảm bảo kết quả nhất quán và chất lượng cao.
Chọn công cụ cắt phù hợp cho công việc
Việc lựa chọn dụng cụ cắt phù hợp là một quyết định quan trọng trong bất kỳ nguyên công gia công nào vì nó ảnh hưởng rất lớn đến chất lượng, hiệu quả và độ chính xác của công việc. Một số yếu tố cần được xem xét khi lựa chọn công cụ cắt thích hợp cho một công việc cụ thể. Dưới đây là hướng dẫn về cách chọn công cụ cắt phù hợp cho dự án gia công của bạn:
1. Chất liệu của phôi:
Vật liệu bạn đang gia công là một trong những yếu tố quan trọng nhất trong việc lựa chọn công cụ. Các vật liệu khác nhau có độ cứng, độ dẫn nhiệt và độ mài mòn khác nhau. Hãy xem xét những điều sau:
- Độ cứng: Các vật liệu cứng như thép cứng hoặc gốm sứ đòi hỏi phải có dụng cụ cắt có cạnh cắt cứng, chẳng hạn như hạt dao cacbua, để chịu được lực cắt cao.
- Vật liệu mềm: Đối với các vật liệu mềm hơn như nhôm hoặc nhựa, thép tốc độ cao (HSS) hoặc các vật liệu dụng cụ khác có thể là đủ.
2. Vận hành gia công:
Thao tác cụ thể mà bạn đang thực hiện, chẳng hạn như tiện, phay, khoan, tiện ren hoặc tạo rãnh, sẽ quyết định loại dụng cụ cắt bạn cần. Các công cụ khác nhau được thiết kế cho các nhiệm vụ khác nhau và việc chọn đúng công cụ sẽ đảm bảo hiệu suất tối ưu.
3. Tốc độ cắt và tốc độ tiến dao:
Xác định tốc độ cắt và tốc độ tiến dao cần thiết dựa trên vật liệu và nguyên công gia công. Các nhà sản xuất dụng cụ cắt đưa ra khuyến nghị cho các thông số này dựa trên thiết kế của dụng cụ và vật liệu được gia công. Tuân thủ các khuyến nghị này là rất quan trọng để đạt được kết quả mong muốn.
4. Hình học công cụ:
Xem xét hình dạng của dụng cụ cắt, bao gồm góc trước, góc hở và bán kính mũi dụng cụ. Hình dạng của dụng cụ phải phù hợp với vật liệu và kiểu cắt. Ví dụ, góc trước dương phù hợp với vật liệu mềm hơn, trong khi góc trước âm sẽ phù hợp hơn với vật liệu cứng hơn.
5. Kích thước phôi:
Kích thước và kích thước của phôi cũng ảnh hưởng đến việc lựa chọn dụng cụ. Một số công cụ cắt phù hợp hơn cho các hoạt động gia công thô để loại bỏ vật liệu rời một cách nhanh chóng, trong khi một số công cụ khác được thiết kế để hoàn thiện nhằm đạt được kích thước và độ hoàn thiện bề mặt chính xác.
6. Yêu cầu về độ hoàn thiện bề mặt:
Nếu bạn yêu cầu một bề mặt hoàn thiện cụ thể, hãy chọn một dụng cụ cắt có hình dạng và độ sắc nét phù hợp. Các công cụ hoàn thiện được thiết kế để mang lại bề mặt mịn hơn, trong khi các công cụ gia công thô sẽ hiệu quả hơn trong việc loại bỏ vật liệu.
7. Chất liệu dụng cụ:
Việc lựa chọn vật liệu dụng cụ là rất quan trọng. Các công cụ cacbua, thép tốc độ cao (HSS), gốm và phủ đều có những ưu điểm và hạn chế. Hãy xem xét các yếu tố như tuổi thọ của dụng cụ, khả năng chống mài mòn và chi phí của vật liệu dụng cụ trong quyết định của bạn.
8. Chất làm mát và bôi trơn:
Xem xét liệu hoạt động cắt có cần chất làm mát hoặc bôi trơn hay không. Một số vật liệu tạo ra nhiệt quá mức trong quá trình gia công và việc sử dụng chất làm mát hoặc chất bôi trơn phù hợp có thể kéo dài tuổi thọ dụng cụ và cải thiện hiệu suất cắt.
9. Lớp phủ dụng cụ:
Nhiều dụng cụ cắt hiện đại đi kèm với lớp phủ chuyên dụng như TiN (Titanium Nitride) hoặc TiAlN (Titanium Aluminium Nitride) để cải thiện khả năng chống mài mòn và giảm ma sát. Chọn một công cụ có lớp phủ thích hợp cho ứng dụng cụ thể của bạn.
10. Cân nhắc chi phí:
Cân bằng chi phí của dụng cụ cắt với hiệu suất và tuổi thọ của nó là rất quan trọng. Mặc dù các công cụ cao cấp có thể mang lại tuổi thọ công cụ dài hơn và hiệu suất tốt hơn nhưng điều cần thiết là phải tìm được sự cân bằng phù hợp với ngân sách dự án của bạn.
11. Khả năng tương thích của hộp đựng dụng cụ và máy:
Đảm bảo rằng dụng cụ cắt đã chọn tương thích với hệ thống giá đỡ dụng cụ của máy tiện hoặc trung tâm gia công của bạn. Giá đỡ dụng cụ phải mang lại sự ổn định và độ cứng cho dụng cụ cắt trong quá trình gia công.
Cuối cùng, công cụ cắt phù hợp cho công việc sẽ phụ thuộc vào sự kết hợp của các yếu tố này. Luôn tham khảo khuyến nghị của nhà sản xuất dụng cụ và cân nhắc tìm kiếm lời khuyên từ các thợ máy hoặc chuyên gia về dụng cụ có kinh nghiệm nếu bạn không chắc chắn. Lựa chọn và thiết lập công cụ phù hợp là nền tảng để đạt được kết quả gia công hiệu quả và chính xác.
Thiết lập công cụ cắt tiện
Thiết lập một công cụ cắt máy tiện để tiện CNC là một quá trình có hệ thống bao gồm một số bước quan trọng. Mỗi bước đều quan trọng để đảm bảo rằng dụng cụ cắt được định vị và căn chỉnh chính xác, cuối cùng dẫn đến gia công chính xác và hiệu quả. Chúng ta hãy thực hiện từng bước quy trình:
Bước 1: Chuẩn bị máy tiện và phôi
Trước khi bạn có thể thiết lập dụng cụ cắt, điều cần thiết là phải chuẩn bị cả máy tiện và phôi:
- Cố định phôi: Đảm bảo phôi được kẹp chắc chắn trong mâm cặp hoặc ống kẹp máy tiện. Đảm bảo rằng nó quay trơn tru mà không bị lắc lư hoặc rung lắc.
- An toàn: Đảm bảo áp dụng tất cả các biện pháp an toàn, bao gồm việc sử dụng thiết bị bảo hộ cá nhân (PPE) thích hợp và cài đặt máy tiện chính xác.
Bước 2: Chọn Giá đỡ công cụ chính xác
Giá đỡ công cụ là một thành phần quan trọng trong quá trình thiết lập. Chọn giá đỡ dụng cụ thích hợp dựa trên các yếu tố như loại dụng cụ cắt, nguyên công được thực hiện và hệ thống trụ dụng cụ của máy tiện.
- Ghép Giá đỡ Dụng cụ với Dụng cụ Cắt: Đảm bảo rằng giá đỡ dụng cụ tương thích với loại và kích thước của dụng cụ cắt mà bạn định sử dụng.
- Độ cứng của giá đỡ dụng cụ: Chọn giá đỡ dụng cụ mang lại sự ổn định và độ cứng. Điều này đặc biệt quan trọng trong các ứng dụng có độ chính xác cao.
Bước 3: Lắp dụng cụ cắt
Việc lắp dụng cụ cắt bao gồm việc cố định dụng cụ cắt vào giá đỡ dụng cụ và đảm bảo dụng cụ được đặt chắc chắn và chính xác:
- Cố định dụng cụ cắt: Lắp dụng cụ cắt vào giá đỡ dụng cụ và siết chặt mọi cơ cấu kẹp, chẳng hạn như vít định vị hoặc ống kẹp. Đảm bảo dụng cụ được giữ chắc chắn.
- Sự định hướng: Xác minh rằng dụng cụ cắt được định hướng chính xác so với phôi. Dụng cụ phải được định vị để tiếp xúc phôi ở góc và độ sâu mong muốn.
Bước 4: Điều chỉnh chiều cao công cụ và căn chỉnh đường tâm
Chiều cao dao chính xác và căn chỉnh đường tâm là rất quan trọng để đạt được kích thước gia công chính xác:
- Điều chỉnh chiều cao công cụ: Điều chỉnh chiều cao của dụng cụ để căn chỉnh nó với đường tâm trục chính của máy tiện. Sử dụng thước đo chiều cao dụng cụ hoặc thanh kiểm tra để đặt dụng cụ ở độ cao chính xác.
- Căn chỉnh đường trung tâm: Đảm bảo rằng dao được căn chỉnh với đường tâm trục chính của máy tiện. Việc căn chỉnh sai có thể dẫn đến gia công lệch tâm, ảnh hưởng đến độ chính xác của bộ phận.
Bước 5: Thiết lập công cụ bù bán kính mũi
Đối với tiện CNC, việc bù bán kính mũi dao sẽ tính đến hình dạng của dụng cụ cắt. Điều này đặc biệt quan trọng khi sử dụng các công cụ chèn:
- Xác định bán kính mũi dao: Đo hoặc tra cứu bán kính mũi chính xác của hạt dao cắt mà bạn đang sử dụng.
- Nhập giá trị bán kính: Trong phần mềm điều khiển CNC, nhập giá trị bán kính mũi dao đo được để đảm bảo máy bù cho hình dạng của dao khi gia công.
Bước 6: Thiết lập offset công cụ
Độ lệch dụng cụ giải thích cho sự thay đổi về kích thước dụng cụ và hình dạng phôi. Chúng đảm bảo rằng vị trí của dụng cụ được điều chỉnh chính xác để gia công:
- Chọn Offset Công cụ Chính xác: Xác định giá trị bù dao thích hợp dựa trên hình dạng của dao và nguyên công gia công. Giá trị bù đắp này bù đắp cho bất kỳ sự khác biệt nào.
- Nhập giá trị bù đắp: Nhập các giá trị offset đã chọn vào phần mềm điều khiển CNC. Các giá trị này sẽ hướng dẫn máy cách điều chỉnh vị trí của dụng cụ một cách chính xác.
Trong suốt quá trình thiết lập công cụ, hãy sử dụng các công cụ đo chính xác như micromet, thước đo chiều cao và chỉ báo quay số để xác minh và tinh chỉnh căn chỉnh công cụ. Thường xuyên kiểm tra và bảo trì dụng cụ cắt để đảm bảo nó luôn sắc bén và ở tình trạng tốt, vì một công cụ được bảo trì tốt sẽ góp phần mang lại kết quả gia công ổn định và chính xác.
Việc thiết lập đúng công cụ cắt máy tiện trong các bước này là rất quan trọng để đạt được kết quả tối ưu trong nguyên công tiện CNC. Độ chính xác và sự chú ý đến từng chi tiết trong quá trình thiết lập công cụ là những yếu tố then chốt để tạo ra các bộ phận gia công chất lượng cao.
Tối ưu hóa các thông số cắt cho tiện CNC
Tối ưu hóa các thông số cắt là điều cần thiết để đạt được các nguyên công tiện CNC hiệu quả và chất lượng cao. Bốn khía cạnh chính cần xem xét khi tối ưu hóa các thông số cắt là tốc độ và bước tiến, độ sâu cắt, chất lỏng cắt và chất bôi trơn cũng như quản lý tuổi thọ dụng cụ.
1. Tốc độ và nguồn cấp dữ liệu:
- Một. Tốc độ cắt (Tốc độ bề mặt):Tốc độ cắt, thường được gọi là tốc độ bề mặt, là tốc độ mà phôi và dụng cụ cắt tương tác với nhau. Nó được đo bằng feet bề mặt trên phút (SFM) hoặc mét trên phút (m/phút). Để tối ưu hóa tốc độ cắt, hãy xem xét vật liệu được gia công và vật liệu của dụng cụ. Ví dụ, các công cụ bằng thép tốc độ cao (HSS) có tốc độ cắt được khuyến nghị thấp hơn so với các công cụ cacbua. Tham khảo dữ liệu của nhà sản xuất công cụ hoặc sổ tay gia công để xác định tốc độ cắt được khuyến nghị cho các vật liệu và dụng cụ cụ thể.
- b. Tỷ lệ thức ăn:Tốc độ tiến dao là tốc độ tuyến tính mà tại đó dụng cụ cắt tiến vào phôi. Nó được đo bằng inch trên mỗi vòng quay (IPR) hoặc milimet trên mỗi vòng quay (mm/vòng). Để tối ưu hóa tốc độ tiến dao, hãy xem xét các yếu tố như đặc tính vật liệu, hình dạng dụng cụ và độ hoàn thiện bề mặt mong muốn. Tốc độ tiến dao cao hơn thường có năng suất cao hơn nhưng có thể yêu cầu dụng cụ chắc chắn hơn.
- c. Mối quan hệ giữa tốc độ cắt và tốc độ tiến dao:Cân bằng tốc độ cắt và tốc độ tiến dao là rất quan trọng để loại bỏ vật liệu hiệu quả. Việc tăng tốc độ cắt thường cho phép tốc độ tiến dao cao hơn, nhưng cả hai phải được điều chỉnh cùng nhau để tránh mài mòn dụng cụ và quá nóng.
2. Độ sâu cắt:
- Một. Độ sâu cắt (DOC):Độ sâu cắt là khoảng cách mà dụng cụ cắt xuyên qua phôi. Điều cần thiết là phải xem xét khả năng của vật liệu và dụng cụ. Tối ưu hóa độ sâu cắt dựa trên độ cứng của vật liệu cũng như độ bền và độ cứng của dụng cụ. Có thể cần cắt nông đối với vật liệu cứng hơn, trong khi có thể cắt sâu hơn đối với vật liệu mềm hơn.
- b. Độ sâu cắt hướng trục và hướng kính:Khi tiện CNC, hãy xem xét cả chiều sâu cắt dọc trục (dọc theo chiều dài phôi) và hướng tâm (ngang qua đường kính phôi). Độ sâu tối ưu cho mỗi loại sẽ khác nhau tùy theo hoạt động và vật liệu.
3. Chất lỏng cắt và chất bôi trơn:
- Một. Chọn chất lỏng cắt phù hợp:Chất lỏng cắt rất cần thiết để tản nhiệt, giảm ma sát và cải thiện khả năng thoát phoi. Chọn chất lỏng cắt thích hợp dựa trên vật liệu và hoạt động gia công. Chất làm mát hòa tan trong nước, chất làm mát gốc dầu khoáng hoặc chất làm mát tổng hợp có thể được ưu tiên cho các vật liệu khác nhau.
- b. Ứng dụng phù hợp:Áp dụng chất lỏng cắt một cách hiệu quả vào khu vực cắt để đảm bảo bôi trơn và làm mát đầy đủ. Điều này có thể được thực hiện thông qua hệ thống làm mát bằng lũ, hệ thống phun sương hoặc cung cấp chất làm mát thông qua dụng cụ, tùy thuộc vào khả năng của máy.
- c. Giám sát và bảo trì:Thường xuyên theo dõi mức độ, tình trạng và độ nhiễm bẩn của chất lỏng cắt để đảm bảo chúng vẫn hoạt động hiệu quả. Duy trì hệ thống chất lỏng cắt để ngăn ngừa các vấn đề như sự phát triển và suy thoái của vi khuẩn.
4. Quản lý tuổi thọ công cụ:
- Một. Kiểm tra và bảo trì công cụ:Thực hiện chương trình kiểm tra và bảo trì công cụ định kỳ để đảm bảo các công cụ ở tình trạng tốt. Dụng cụ cùn hoặc hư hỏng có thể dẫn đến chất lượng gia công kém và giảm tuổi thọ dụng cụ.
- b. Lịch thay thế công cụ:Thiết lập lịch thay thế công cụ dựa trên các yếu tố như độ mòn của công cụ, thời gian hoạt động của máy và yêu cầu sản xuất. Điều này giúp ngăn ngừa các lỗi dụng cụ không mong muốn và duy trì chất lượng gia công ổn định.
- c. Tối ưu hóa tuổi thọ công cụ:Một số vật liệu và lớp phủ dụng cụ có tuổi thọ dụng cụ dài hơn. Hãy cân nhắc sử dụng dụng cụ hiệu suất cao để tối ưu hóa tuổi thọ của dụng cụ và giảm thời gian ngừng sản xuất.
- d. Kiểm soát chip công cụ:Kiểm soát phoi hiệu quả, bao gồm việc sử dụng bộ ngắt phoi và hình dạng dụng cụ thích hợp, có thể kéo dài tuổi thọ của dụng cụ bằng cách giảm mài mòn do phoi gây ra.
Tối ưu hóa các thông số cắt trong tiện CNC là một quá trình liên tục. Có thể cần phải thử nghiệm và tinh chỉnh để tìm ra các thông số tốt nhất cho một ứng dụng cụ thể. Thường xuyên theo dõi và điều chỉnh các thông số này để đảm bảo hiệu suất gia công, tuổi thọ dụng cụ và chất lượng bộ phận tối ưu. Các thông số cắt được tối ưu hóa phù hợp không chỉ cải thiện hiệu quả gia công mà còn giảm mài mòn dụng cụ và cuối cùng là giảm chi phí sản xuất.
Khắc phục sự cố thường gặp trong cài đặt công cụ
Khắc phục sự cố thường gặp trong cài đặt công cụ là một kỹ năng cần thiết đối với thợ máy và người vận hành CNC. Hiểu và giải quyết những vấn đề này có thể giúp duy trì độ chính xác và chất lượng của các hoạt động gia công. Dưới đây là một số vấn đề về cài đặt công cụ phổ biến và giải pháp khắc phục:
1. Trò chuyện về công cụ:
Vấn đề: Tiếng kêu của dụng cụ xảy ra khi dụng cụ cắt rung trong quá trình gia công, dẫn đến độ hoàn thiện bề mặt kém, mòn dụng cụ và có khả năng làm hỏng phôi.
Giải pháp:
- Giảm tốc độ hoặc tăng nguồn cấp dữ liệu: Điều chỉnh các thông số cắt bằng cách giảm tốc độ cắt hoặc tăng tốc độ tiến dao. Sự thay đổi này có thể làm giảm độ rung và giảm tiếng ồn.
- Kiểm tra độ cứng của công cụ: Đảm bảo rằng giá đỡ dụng cụ và dụng cụ được cố định chính xác và dụng cụ không kéo dài quá xa giá đỡ.
- Kiểm tra kẹp phôi: Đảm bảo phôi được kẹp chắc chắn để tránh mọi rung động liên quan đến phôi.
- Sử dụng kỹ thuật giảm chấn: Một số máy có tính năng giảm rung. Nếu có sẵn, hãy cân nhắc sử dụng chúng.
- Chọn một công cụ cứng hơn: Một công cụ cứng nhắc hơn, chẳng hạn như một công cụ có ít sáo hơn, có thể giúp giảm tiếng ồn.
2. Bề mặt hoàn thiện kém:
Vấn đề: Độ hoàn thiện bề mặt kém có thể do các vấn đề về thiết lập dụng cụ hoặc thông số cắt, dẫn đến bề mặt gồ ghề hoặc không nhất quán trên phôi.
Giải pháp:
- Kiểm tra hình học công cụ: Đảm bảo rằng hình dạng của dụng cụ cắt phù hợp với nguyên công. Một công cụ sắc bén với hình dạng chính xác là rất quan trọng để đạt được bề mặt hoàn thiện tốt.
- Tối ưu hóa các thông số cắt: Điều chỉnh tốc độ cắt, tốc độ tiến dao và độ sâu cắt để tìm ra sự kết hợp tốt nhất cho vật liệu và hoạt động cụ thể.
- Kiểm tra độ mòn của dụng cụ: Kiểm tra dụng cụ xem có dấu hiệu mòn hoặc hư hỏng không, chẳng hạn như các cạnh bị sứt mẻ. Thay thế hoặc mài lại dụng cụ khi cần thiết.
- Sử dụng chất lỏng cắt thích hợp: Việc bôi trơn và làm mát thích hợp có thể ảnh hưởng đáng kể đến độ hoàn thiện bề mặt. Sử dụng chất lỏng cắt phù hợp cho vật liệu và hoạt động.
- Giảm thiểu độ rung: Giải quyết các vấn đề rung động để tránh tạo ra sự bất thường trên bề mặt.
3. Sự không chính xác về kích thước:
Vấn đề: Các bộ phận có thể có kích thước không chính xác do dụng cụ bị lệch hoặc dụng cụ bị mòn.
Giải pháp:
- Kiểm tra cài đặt công cụ: Xác minh rằng dụng cụ được thiết lập chính xác với chiều cao và căn chỉnh phù hợp với phôi.
- Hiệu chỉnh máy: Đảm bảo máy CNC được hiệu chỉnh đúng cách và diễn giải chính xác độ lệch dao và dữ liệu dao.
- Điều chỉnh độ lệch công cụ: Sửa bất kỳ lỗi nào trong việc bù dao bằng cách đo chính xác dao và nhập các giá trị bù thích hợp vào bộ điều khiển CNC.
- Kiểm tra độ mòn của dụng cụ: Thường xuyên kiểm tra độ mòn của dụng cụ cắt và thay thế hoặc mài lại khi cần thiết.
4. Vấn đề kiểm soát chip:
Vấn đề: Kiểm soát phoi không đúng cách có thể dẫn đến các vấn đề như tắc phoi, thoát phoi kém và làm hỏng phôi hoặc dụng cụ.
Giải pháp:
- Chọn hình học công cụ phù hợp: Chọn một dụng cụ cắt có hình học hoặc bộ ngắt phoi thích hợp cho vật liệu và nguyên lý hoạt động.
- Tối ưu hóa các thông số cắt: Điều chỉnh tốc độ tiến dao, tốc độ cắt và độ sâu cắt để tối ưu hóa việc hình thành và thoát phoi.
- Sử dụng chất bôi trơn vừa đủ: Việc sử dụng đúng chất lỏng cắt có thể giúp bôi trơn và tạo điều kiện thuận lợi cho việc thoát phoi.
- Kiểm tra sự căn chỉnh của dụng cụ và phôi: Đảm bảo rằng dụng cụ được căn chỉnh chính xác với phôi gia công để ngăn ngừa các sự cố liên quan đến phoi.
5. Hỏng dụng cụ:
Vấn đề: Sự cố gãy dụng cụ có thể xảy ra do lực quá mạnh, thiết lập dụng cụ không chính xác hoặc các vấn đề liên quan đến vật liệu.
Giải pháp:
- Tối ưu hóa các thông số cắt: Giảm lực cắt bằng cách điều chỉnh các thông số như tốc độ tiến dao, tốc độ cắt và độ sâu cắt.
- Kiểm tra cài đặt công cụ: Đảm bảo rằng dụng cụ được lắp chắc chắn vào giá đỡ dụng cụ và được căn chỉnh chính xác.
- Sử dụng vật liệu công cụ thích hợp: Chọn vật liệu dụng cụ phù hợp cho vật liệu cụ thể mà bạn đang gia công. Ví dụ, dụng cụ cacbua tốt hơn cho vật liệu cứng.
- Kiểm tra độ mòn của dụng cụ: Thường xuyên kiểm tra dụng cụ xem có dấu hiệu hao mòn hay không và thay thế nó trước khi nó bị mòn quá mức và dễ bị gãy.
Việc giải quyết các vấn đề về cài đặt công cụ phổ biến này đòi hỏi sự kết hợp giữa đào tạo phù hợp, bảo trì thường xuyên và cách tiếp cận có hệ thống để khắc phục sự cố. Khả năng chẩn đoán và giải quyết các vấn đề liên quan đến dụng cụ là rất quan trọng để đạt được kết quả gia công hiệu quả và chất lượng cao.
Kết luận
Quá trình thiết lập và tối ưu hóa các công cụ cắt máy tiện để tiện CNC là một khía cạnh quan trọng của gia công, tác động đáng kể đến chất lượng, hiệu quả và độ chính xác của quy trình sản xuất. Sự hiểu biết sâu sắc về các thành phần và chức năng của dụng cụ cắt cũng như các yếu tố liên quan đến việc lựa chọn dụng cụ là điều cần thiết đối với thợ máy và người vận hành CNC.
Việc thiết lập đúng dụng cụ cắt bao gồm một cách tiếp cận có hệ thống, từ việc chuẩn bị máy tiện và phôi đến chọn giá đỡ dụng cụ chính xác, lắp dụng cụ, điều chỉnh chiều cao dụng cụ và căn chỉnh đường tâm cũng như cấu hình bù bán kính mũi dao và độ lệch dao. Mỗi bước đóng một vai trò quan trọng trong việc đạt được kết quả gia công chính xác và hiệu quả.
Tối ưu hóa các thông số cắt, bao gồm tốc độ và bước tiến, độ sâu cắt, chất lỏng cắt và quản lý tuổi thọ dụng cụ, là một khía cạnh quan trọng khác của tiện CNC. Bằng cách lựa chọn cẩn thận các thông số phù hợp, thợ máy có thể nâng cao năng suất, duy trì tuổi thọ của dụng cụ và cải thiện chất lượng hoàn thiện bề mặt.
Cuối cùng, khả năng khắc phục các sự cố cài đặt công cụ phổ biến, chẳng hạn như tiếng kêu của công cụ, độ hoàn thiện bề mặt kém, độ không chính xác về kích thước, sự cố kiểm soát chip và gãy dao, là điều cần thiết để duy trì kết quả gia công nhất quán và chất lượng cao. Việc xác định những vấn đề này và thực hiện các giải pháp thích hợp sẽ đảm bảo rằng quá trình gia công vẫn diễn ra suôn sẻ và hiệu quả.
Nhìn chung, sự hiểu biết toàn diện về các công cụ cắt máy tiện và cách thiết lập chúng, kết hợp với khả năng tối ưu hóa các thông số cắt và khắc phục sự cố, giúp các thợ máy đạt được kết quả tốt nhất trong nguyên công tiện CNC. Học tập, đào tạo và trải nghiệm liên tục là chìa khóa để hoàn thiện những kỹ năng này và đảm bảo quá trình gia công thành công.
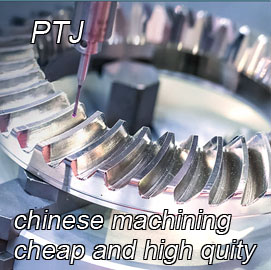
- Gia công 5 trục
- Cnc phay
- Cnc quay
- Công nghiệp gia công
- Quá trình chạy máy
- Xử lý bề mặt
- Gia công kim loại
- Gia công nhựa
- Khuôn luyện kim bột
- Đúc chết
- Phòng trưng bày các bộ phận
- Bộ phận kim loại ô tô
- Bộ phận máy móc
- Tản nhiệt LED
- Bộ phận xây dựng
- Bộ phận di động
- Bộ phận y tế
- Phần điện tử
- Gia công phù hợp
- Phụ tùng xe đạp
- Gia công nhôm
- Gia công titan
- Gia công thép không gỉ
- Gia công đồng
- Gia công đồng thau
- Gia công siêu hợp kim
- Gia công Peek
- Gia công UHMW
- Gia công Unilate
- Gia công PA6
- Gia công PPS
- Gia công Teflon
- Gia công Inconel
- Gia công thép công cụ
- Vật liệu khác